Yes, sorry for delay, managed to get a tail section out, did a much lighter lay-up, 1 300csm +2x 450 + 1 380 2x2 twill and it does seem about right, suspect I will do another front section to this spec. Enough gassing, some pics for you.
first one is of it laid up ready to be released

rear section
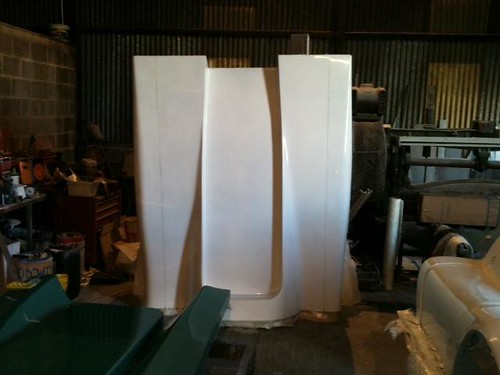
close up, needs a good trim etc yet

So this will be the end of the fibreglassing for a while now, have a spaceframe to make but will keep you updated with progress from time to time
I do and will post pics on my Flickr page http://www.flickr.com/photos/47153142@N03/sets/72157623861979360/
best regards Chris