The title of this thread is confusing as we are (I think) talking about a replacement roof panel not a roof cap.
We make infused CF roofs occasionally, material costs aren’t so bad as we use:
2 x 2by2 twill
2mm infusion coremat
woven roving (FG)
Black Diolen.
The black Diolen (like Kevlar) is used to hold the thing together in the event of an accident, protect the occupants and also to stop any corrosion which may be caused by putting CF against steel.
We make them because OE roofs aren’t available any more, are known for rusting and also many are sunroof equipped which make them very heavy - ours aren’t of course being both a lot lighter and stronger. People get rid of OE roofs due to rust and because you can’t get a cage in a sunroof equipped car.
I made the mould for myself really (for a project I’m slowly building), and just use it to knockout the odd roof to help pay for it, it is a three part mould.
They fetch good money, but only occasionally sell.
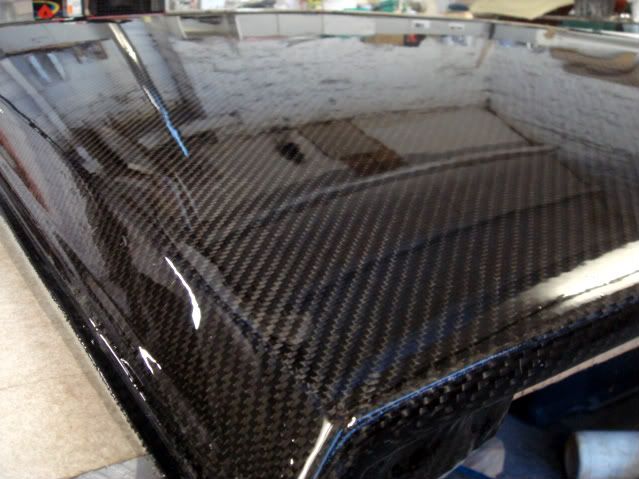
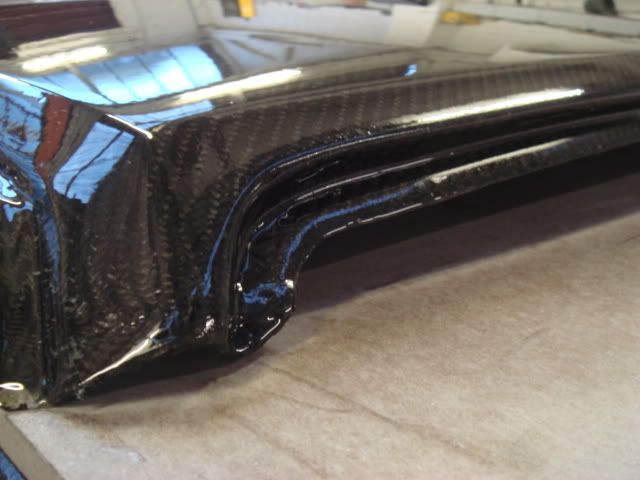