Degassing your resin is just good practice, just like the cup transfer method where you pour your mixed resin into another clean cup. It’s not necessary but it helps you control as many aspects of your layup as possible. This is particularly important on structural parts.
Recently I worked on a project to make carbon fiber wheel shells using a resin infusion method. For this I degassed my resin for approximately 3-5 minutes after mixing it in my catch pot. Depending on your resin system you’ll definitely notice a difference.
(BEFORE)
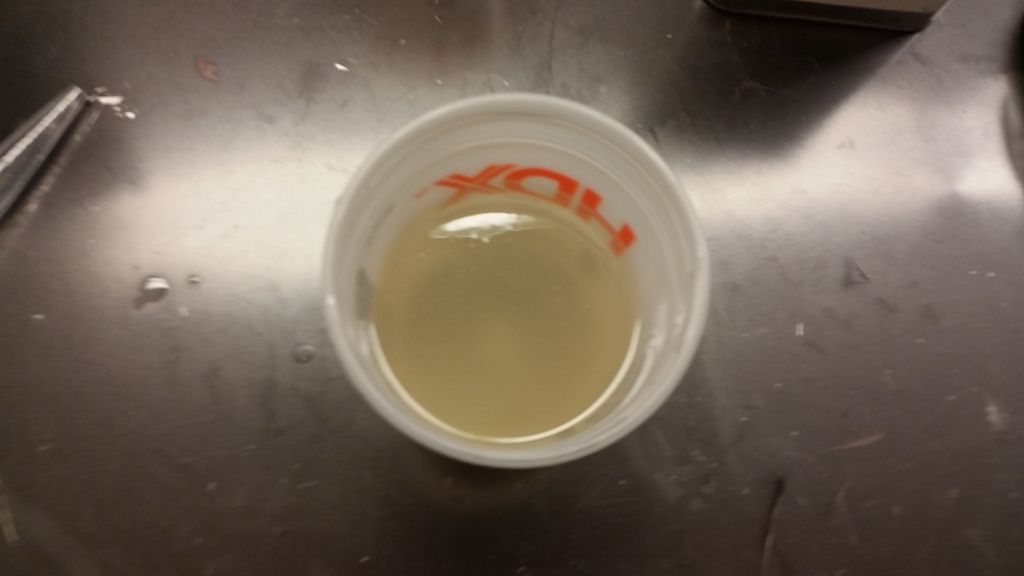
(AFTER)
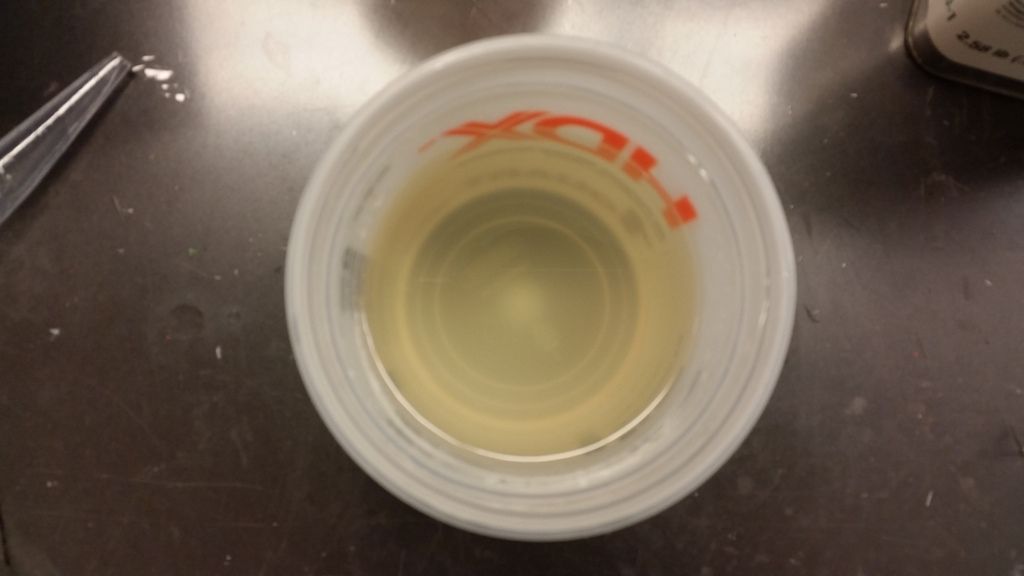
After degassing I noticed fewer micro bubbles in my resin which means less air in your final part. My advice get your self a designated degassing chamber so you don’t have to unhook your catch pot from infusion part and vacuum pump. I made one for about $50 using a kitchen pot and a 1/2" thick clear plexiglass plate.
Its best to have a clear top so you can observe the resin degas, as the pressure in the vacuum chamber decreases the resin will start to foam at the top. Once this top foam layer has collapsed you know your resin has been properly degassed. Depending on the resin system that can take anywhere from 2-5 minutes.
Couple things to remember, don’t leave the resin in the chamber for much longer than 5 minutes because it might exotherm too much. I usually give the resin a quick stir after degassing (being carful not to mix more air in) to even out the temperature. Finally drop and raise the pressure in the chamber slowly, like full vacuum over 30ish seconds, otherwise you might splash the resin out of the cup either by air rushing in too quickly or air foaming out of the resin too quickly.
Good luck!