With the four values shown above, young’s moduli, shear modulus, poisson’s ratio, it is now possible to calculate the reactions to in plane loads. This section requires a grasp of matrix algebra, I will try and take it slow but you may need to review your matrix multiplication rules.
This next section will be pretty difficult to understand going forward but I will present it this way since it’ll make the most sense later. I HIGHLY suggest that you skim this section the first time, read forward a bit, and then come back and reread this when you feel comfortable.
General Compliance Matrix
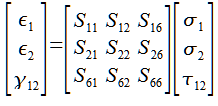
This is the general form for the compliance matrix. It is called the compliance matrix because it shows how much the material complies, or deforms, under a load. The stress values on the right are multiplied by the compliance matrix to show the strains on the right. The values on the left of the equal sign are strains, the sigma’s and tau on the far right are stresses. It is important to note that those two are environmental variables. The values that describe the composites are all the variables in the S matrix, or the center one with all the S’s.
You can see that 9 variables are needed to fully describe the composite in this case
Uncoupled Compliance Matrix
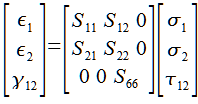
When a fiber reinforced composite is loaded in the fiber direction you lose the shear coupling terms. Every value that coupled the shear stress with a linear strain is now zeroed out.
With the removal of the coupling terms you can see that 5 variables are needed to describe the composite
Reduced Compliance Matrix
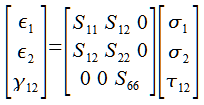
By exploiting one last relationship we can remove one more variable. The more subtle change this time is S12 and S21. By doing some math it has been shown that these two are equal. If you’re feeling brave you may verify this by using the work energy theorem. In general with in plane loading of composites the following relationship holds.

So with the reduced matrix above it only takes 4 variables to describe the in plane loading of a unidirectional composite material. Thankfully the calculation of those variables is quite simple.
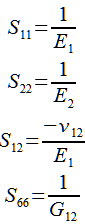
These formula’s are actually the same ones we saw in the materials engineering thread, the only difference here is the lack of stress. However as you’ll soon see these terms combine with the stress terms to produce identical equations to the loading we described before. I don’t expect all of you to see this instantly so in the next post I will go step by step in explaining how all these variables come together.