First I made a mould for the neck by cutting the shape out of 2 sheets of 12mm MDF. I used a router to shape the sides and angle them out at 10 degrees. Then glued each sheet onto another uncut sheet to give me 2 mirrored cavity’s. I then got these sprayed with 2k primer.
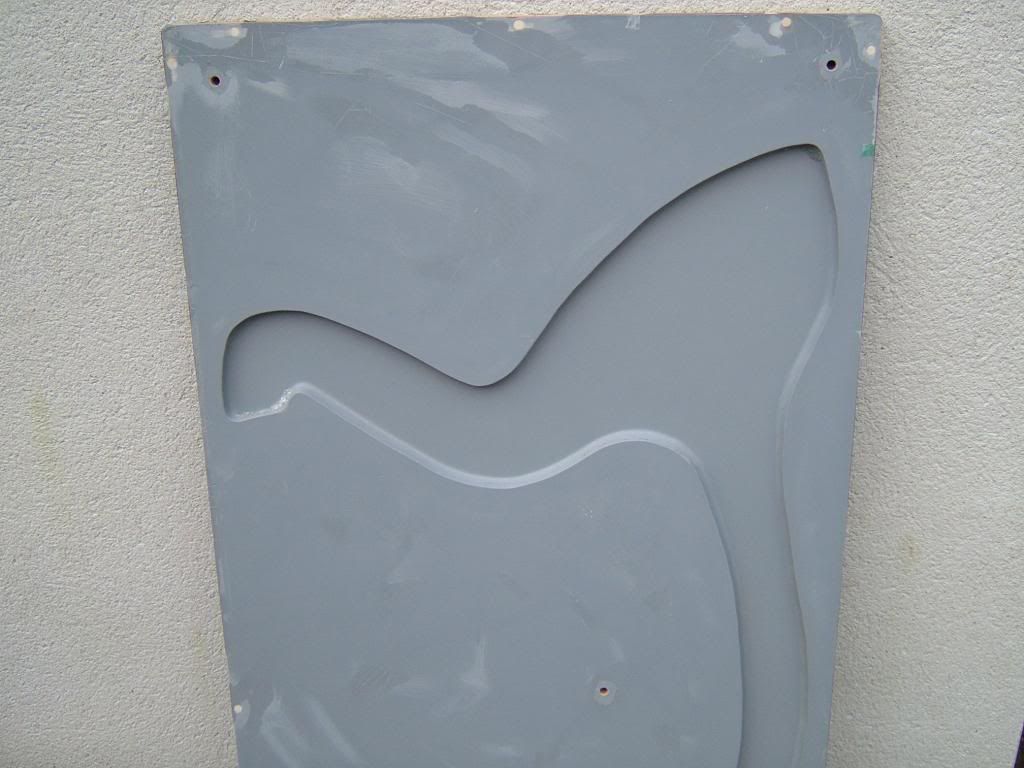
I was hoping to use this as a mould and tested it first using Fibreglass as it is a lot cheaper than Carbon Fibre. This mostly worked but it did damage the MDF and the finished piece was not as smooth as I would have liked. Rather than start again I cleaned up the 2 Fibreglass sides. Used filler to smooth them off and improve the shape. Then made plastic locating pegs to fit the 2 sides together. I used silicon sealant to bond one side, cavity down onto a board. Then used Easy Composites’ Uni-Mould system to make one half of a new mould from this. When this was set I removed it from the board.
[URL=[IMG]http://i1269.photobucket.com/albums/jj586/BrianSaville/DSCF5397.jpg[/IMG]
Without removing the Fibreglass part I cleaned it up The white dots are modelling clay which I removed to make locating pins for the mould. I fitted the other Fibreglass side to this and made the second half of the mould.
Taking the 2 new moulds, I painted them with Gel coat then laid up the Carbon Fibre and foam core material and infused them.
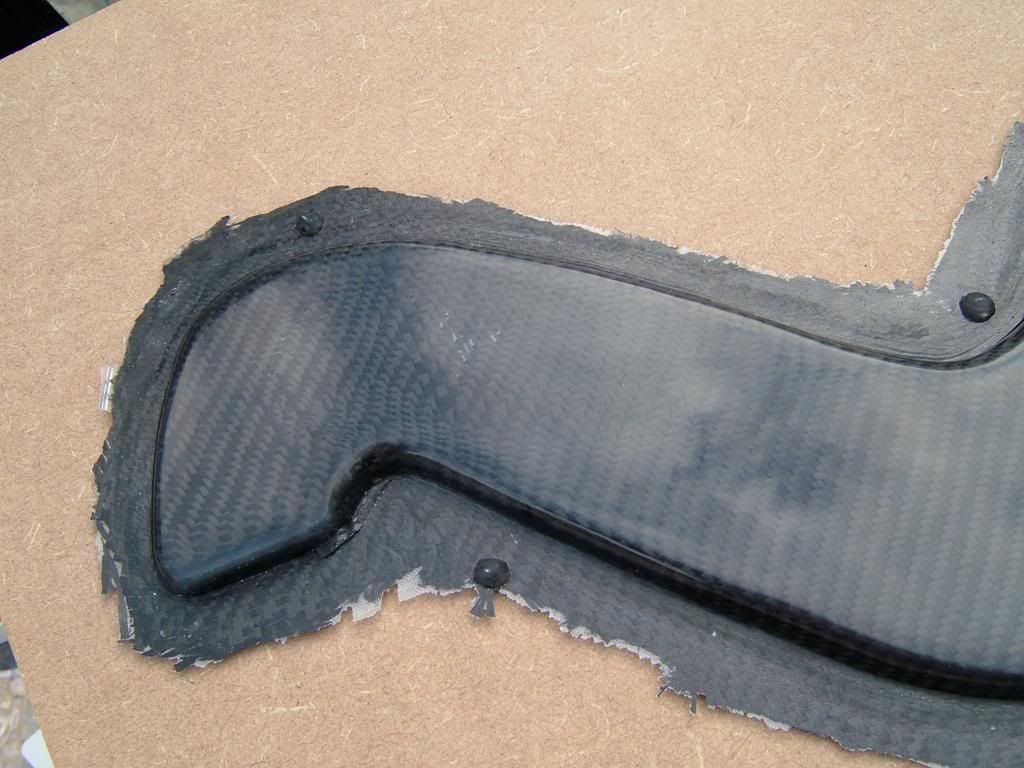
I trimmed these up to fit together.
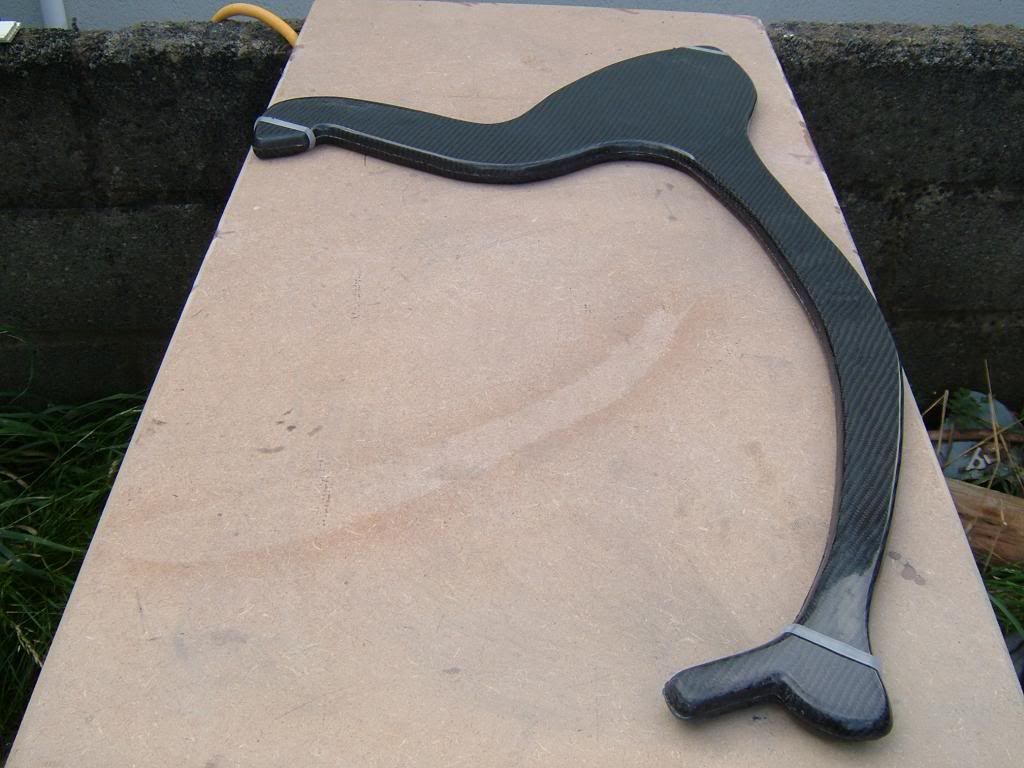
Then put them back into their moulds and bonded them together with a polyurethane adhesive. This left a bond line that needed cleaning up so I sanded it down and painted gel coat over it.
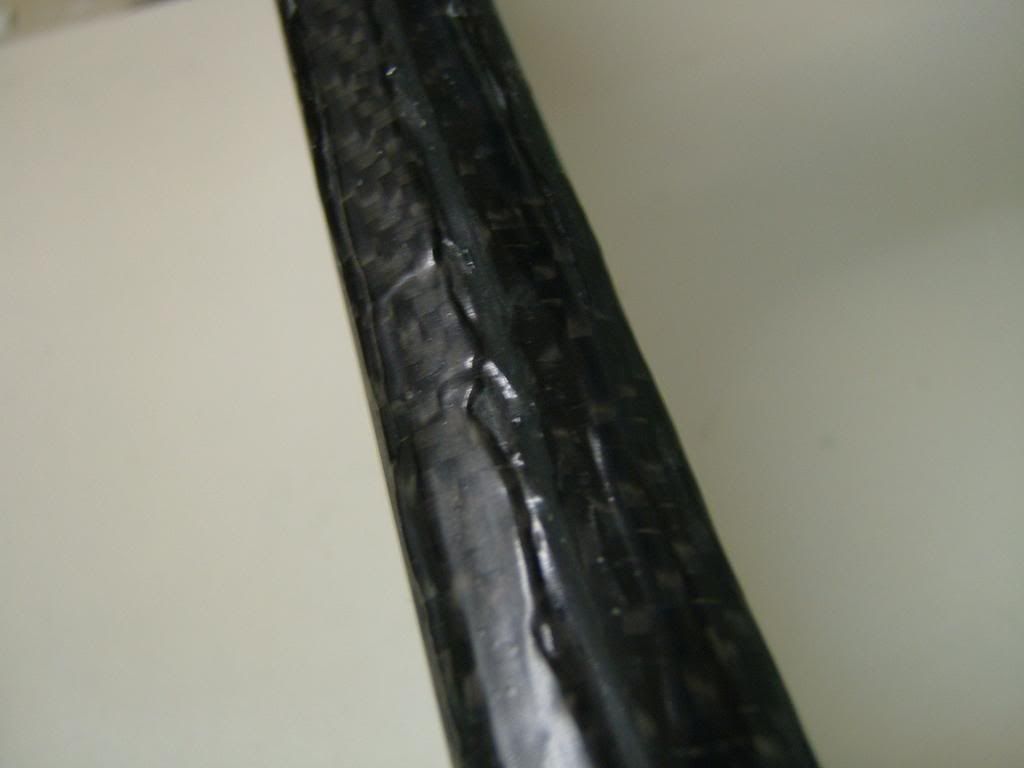
When finished and polished it looks OK.
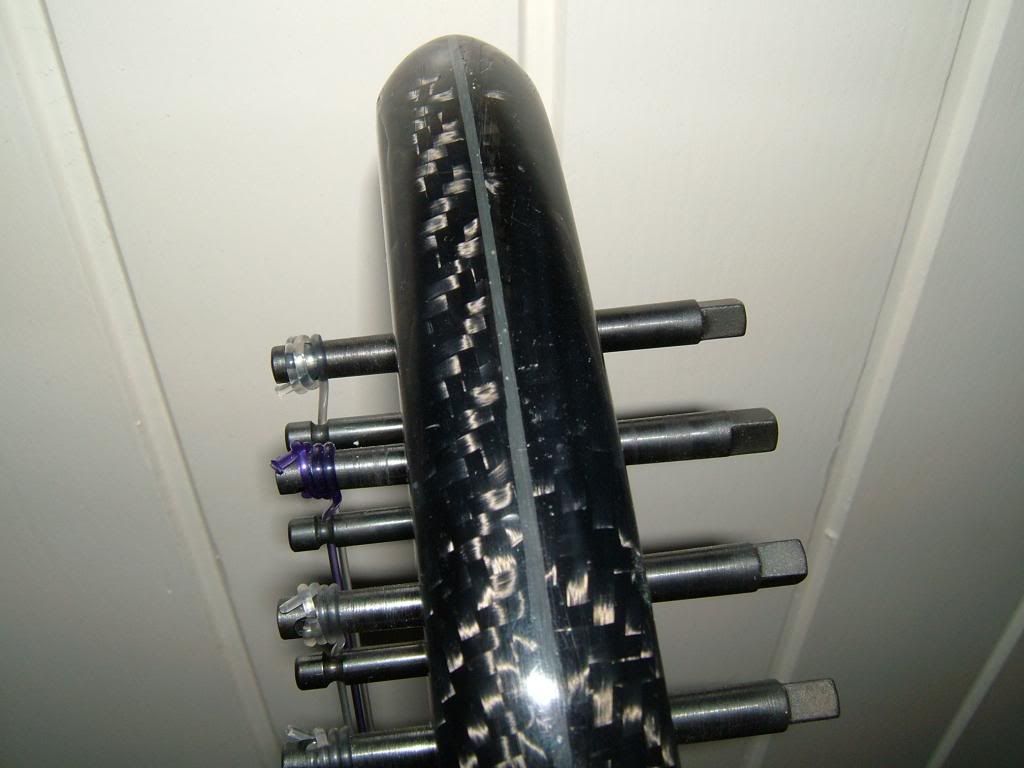
I then drilled this out to fit the tuning and bridge pins.
The sound box was made by infusing the parts on a glass sheet. I wanted a rounded corner on the sides so I found some Bath edging strip in a DIY store, bonded this to the glass and infused over it. The sides are strengthened with 5mm foam.
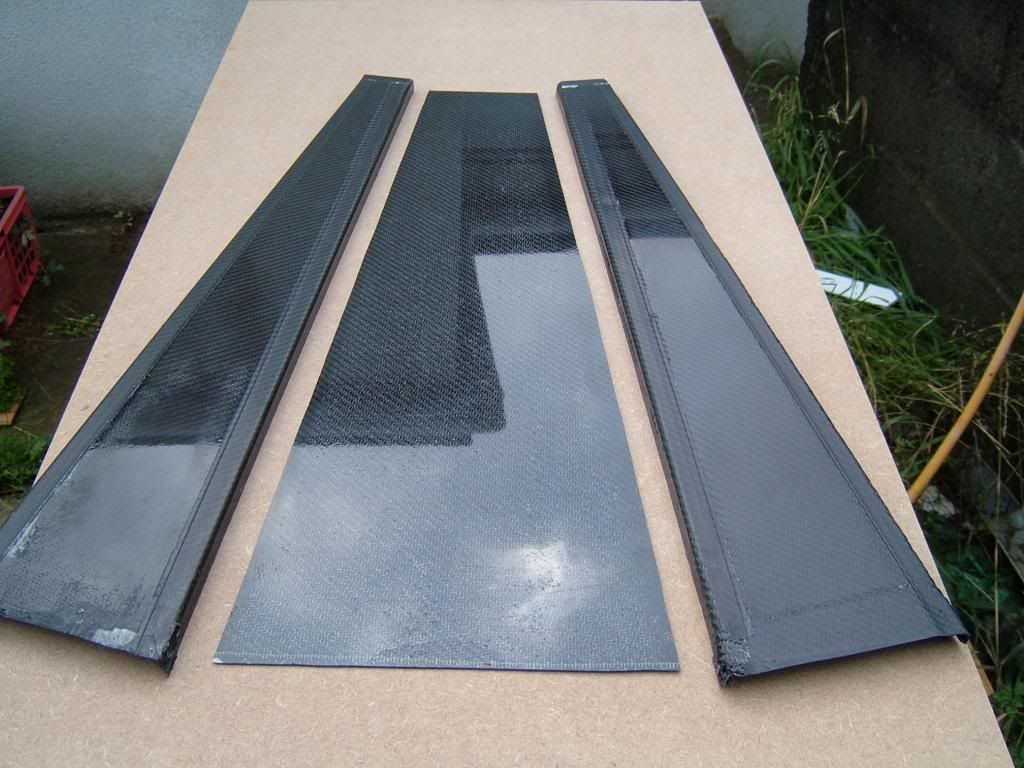
Most of the ragged bit at the bottom of the sides was trimmed off. I thought it would be easier to make them and cut them to size rather than try to mirror the angles and get the lengths matching. Where the edging strip was it was a bit sharp and rough. I painted Gel coat over this and sanded it down. This was lots of work and did not give a perfect finish but I decided it was good enough or at least as good as I would get it.
The sound board has a rib down the back to strengthen it where the strings go through. I used 5 mm foam to make this.
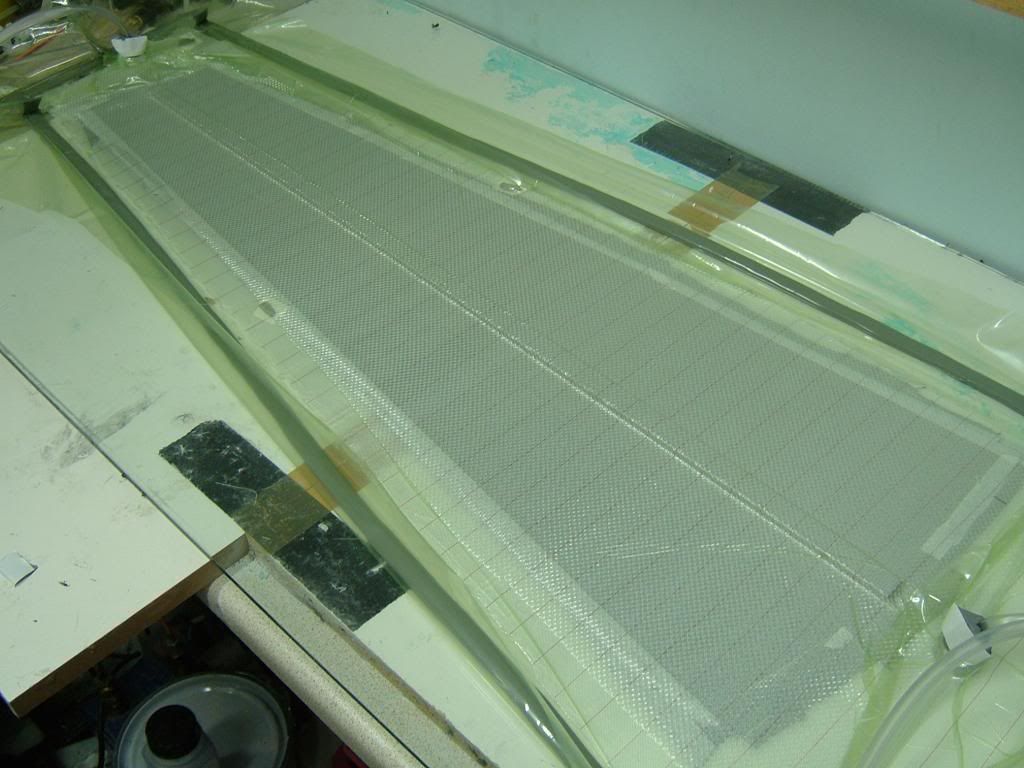
I then bonded it all together with the same polyurethane adhesive.
I was worried about it taking the strain of the pull from the strings. This is about 660 lb. This does not sound much but imagine 4 men standing on it!
Brian.