Hello everyone,
New update today. I was able to do two small sheets for testing new techniques today.
Here are the two plates out of the oven.
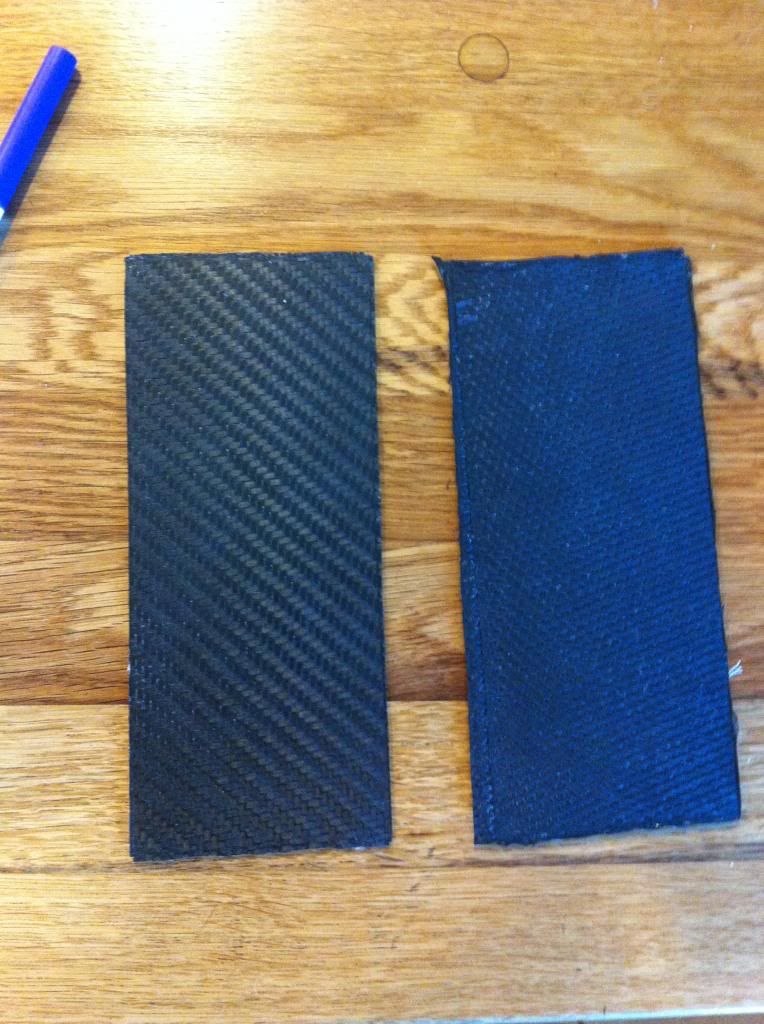
The layup was relatively simple. I used a 5.7 ounce 2X2 twill weave for one and I believe a satin fabric with a definitely heavier tow, as the final product was noticeably thicker than the twill one.
The two test pieces were 3"x7", with 5 layers each, They were placed on a waxed 1/8" thick aluminum plate.
I only used non-perf release film on the CF, I also used little strips of peel ply in place of glass tow to hopefully help extract the air from the material. The peel ply strips were connected to breather that was on the perimeter of the plate.
I debulked the 5 layers of prepreg for an hour and a half at room temperature.

I then ramped it up to 150F and had it dwell for 90 minutes. Next, I ramped it up to 300F and held it for 4 hours and then I let the part cool down to 140F.
Here is the whole thing just out of the oven.
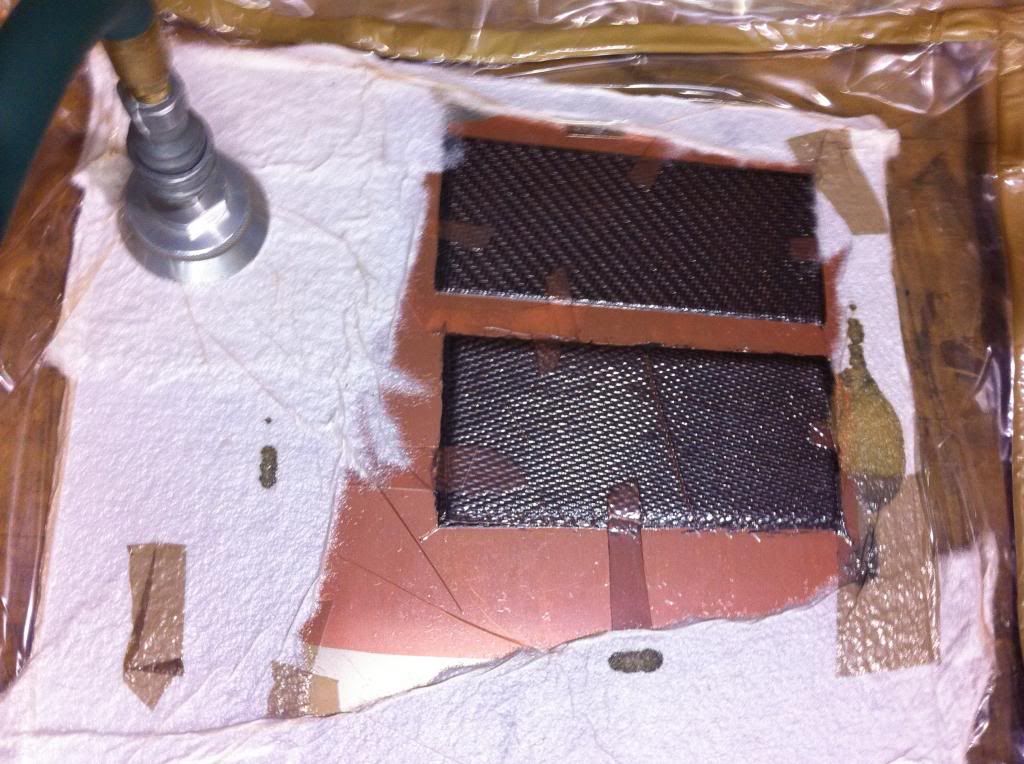
Right off the bat i noticed that the vacuum bag and relase film got sucked in between the fibers of both materials. I was alittle dissapointed in that part. I did notice however that where the peel ply strips were, they had a more uniform surface than the rest of the part.
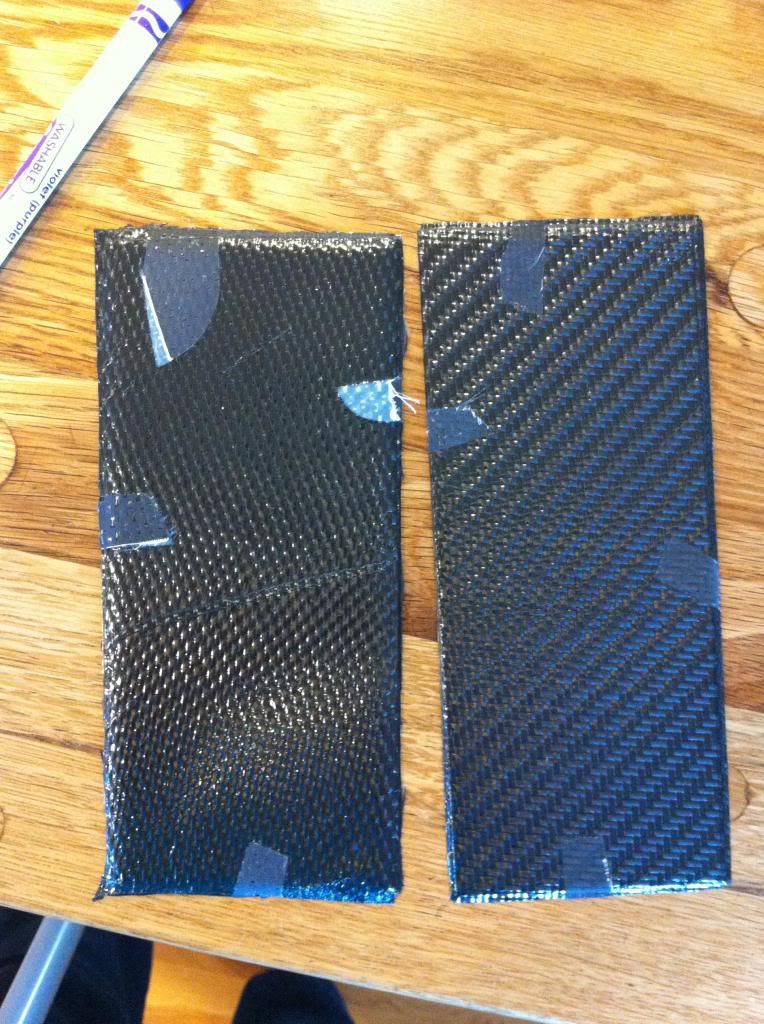
The tool side of the part was more interesting. The satin weave prepreg did not do as well as i expected. It was about the same, if not worse than the little box i made. I believe that prepreg had a higher resin system than the twill weave one. I think that is the reason why it did not do so well, and the fact that it had a thicker, heavier weave to it. This means less compaction of the fibers.
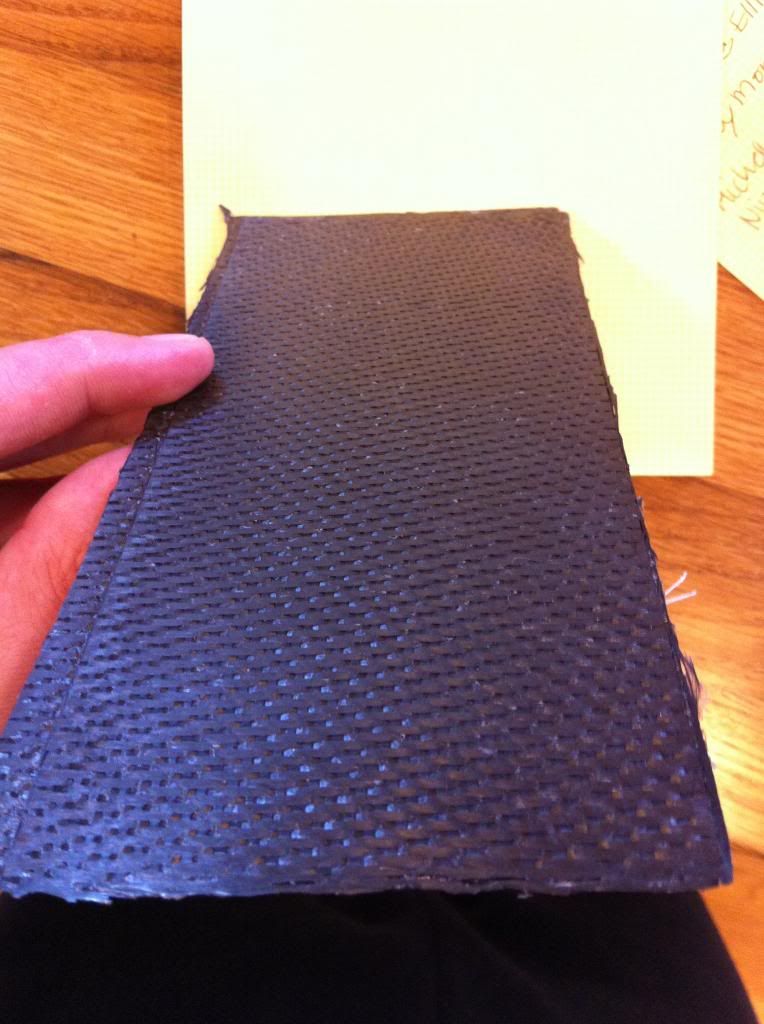
The twill weave prepreg turned out a lot better. I was expecting the material to be worse than the satin weave in terms of surface finish. The twill weave had much shallower voids on the surface, some portions have no surface voids at all which is kinda cool. The finish isn’t autoclave class by any means, but I do believe that it would only take a single coat of lacquer to fill in the gaps on this part.
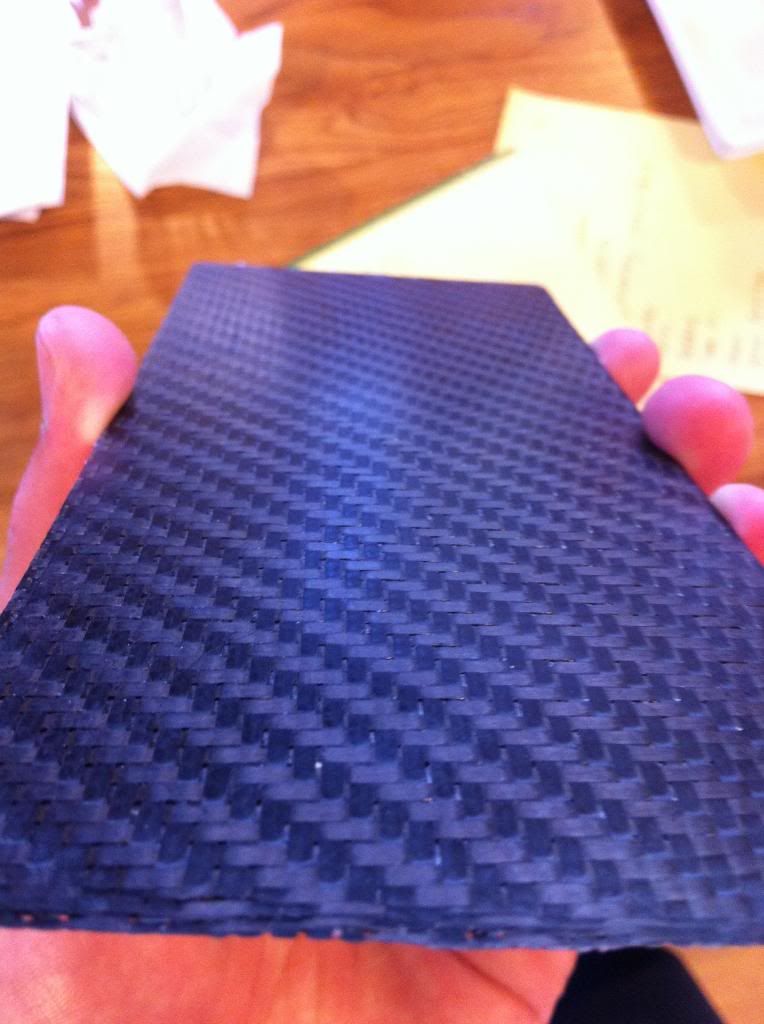
I am not satisfied yet, I want to experiment with different combos of breather, peel ply, and release film. I did not debulk in between layers. I think I’ll try to do that next time. Most likely after the second layer.
Let me know what you guys think.